Tips & Tricks
Complementary Machining - Part 1
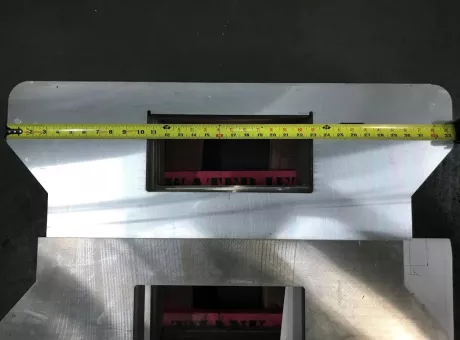
Every precision CNC machine shop contains multiple types of equipment. They often utilize mills, lathes, multi-axis machine centers, grinders, EDM machines and precision hones. The goal of any machine shop is to add value to a product through the manufacturing process. Abrasive waterjet machines should have a common place within a machine shop because they add value by eliminating non-value-add time and creating geometry that is both common and/or not possible with traditional CNC machines. In part one of Complementary Machining, we’ll take a look at how the precision and speed of abrasive waterjet makes it a perfect fit into any machine shop.
The average machine shop sometimes views waterjet as a low precision device – only rough cutting as a material-prep operation. However, that would be misconception. At the OMAX Corporation’s facility in Kent, Washington, we have a waterjet center that produces parts use in manufacturing our waterjets. The waterjet cell has produced and maintained over three-hundred-thousand 1.5” thick, heat-treated, 4340 steel motor plates all within 0.005” tolerance. This tolerance is straight off the waterjet without any secondary machining.
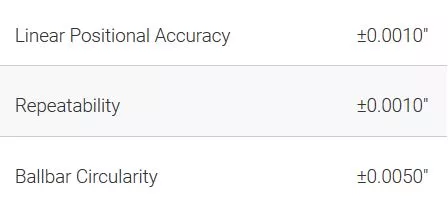
As a standard, the OMAX line of waterjets maintains a range of accuracies rivaling any common commercial machine tool.
This precision is achieved through linear encoder drive systems, software cutting models, ridged construction, and OMAX’s direct drive pump system. The direct drive pumps allow for less fluctuation in the cutting stream, resulting in a steadier, more consistent jet stream.
Not only is a waterjet a precision cutting tool, it is also very fast compared to traditional CNC machines. The part shown below was a simple geometric piece cut from 1 ¼” 6061 T6 aluminum.
When CNC machining, raw material has to be turned into chips, as the mill doesn’t do a very good job removing a chunk of material like a waterjet or a saw does. Adding in the cycle time to turn both external chunks and internal windows into chips could drive a mill-only solution to a cycle time twice that of the waterjet.
As you can see from the table above, the set-up time is drastically less when using a waterjet. Since an OMAX waterjet does not have any heavy, cumbersome, or time consuming fixturing the setup is relatively easy. Material, usually plate, is set on the abrasive waterjet’s cutting table and clamped into place. That’s it. Traditional CNC machines can average 2.5 hours per job setup. Each type of CNC utilize their own work holding devices that are usually extremely heavy to standup to the physics of working within the machine. In addition, CNCs often need several cutting tools for a single part. All of these tools need to be loaded into the respective CNC machine and referenced.
In next month’s Complementary Machining, we’ll look at the advantages waterjet has in software and waste material.