Customer Success: Cutting Services
Venables Machine Works Trusts Their OMAX 55100 for Quick Turnarounds
Machine: OMAX 55100

Off the Trans-Canada Yellowhead Highway in Saskatoon, Saskatchewan, Venables Machine Works Limited takes advantage of abrasive waterjet technology to beat tight turnaround times. “Meeting tight delivery deadlines helps promote Venables as a shop that will manufacture on time and on budget,” states Dan Wingerak, Venables’ Shop Manager and Vice President of Operations.
Venables Machine Works started in 1931 by Hector Venables. Since then the shop has been owned and operated by employees buying into the company. Over eighty years later, Venables has grown into a 70-person custom manufacturing and fabrication shop specializing in steel. Being in the heart of POW country (potash, oil, and wheat), the shop serves the surrounding area with engineering, fabrication, and materials cutting services.
In 2011, Venables purchased their OMAX 55100 JetMachining Center®. “We found that we were outsourcing a lot of profile cutting and determined that purchasing a profiling machine could pay for itself in a couple years,” says Wingerak. “When deciding between a flame, plasma, laser, or waterjet, we decided to go with the waterjet due to the precise cutting option with no heat or heat affected distortion, the ability to cut almost any type of material.” In addition, abrasive waterjet conserves time by removing the need for secondary machining.
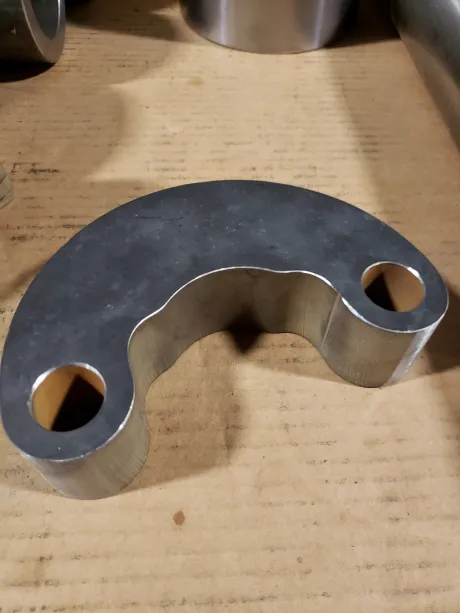
Adding the abrasive waterjet to an already impressive shop floor of CNC mills, lathes, and plate rolls, kept Venables competitive in a time sensitive market. “Having our own machine allows us to respond to customer inquiries without the delay of outsourcing,” says Wingerak. “A considerable portion of our projects are time sensitive and having the OMAX waterjet allows us to respond in a timely manner, which many of our competitors are unable to provide a completed product as quickly or accurately.” With more profiling being cut in-house, as opposed to being subcontracted, Venables fabrication projects have become faster with more exact precision.
As part of purchasing their OMAX 55100, the Venables’ team elected to participate in the OMAX training. “Thomas Dunlap was our Technical Trainer and was extremely knowledgeable about operation of the OMAX Machine and the required maintenance,” says Wingerak. “Thomas provided a very thorough training and, upon return to Venables, we had the awareness required to successfully operate our OMAX 55100 and train our employees.” Having the training coincide with the installation of their abrasive waterjet, Venables wasted no time in utilizing the benefits of abrasive waterjet. OMAX training is conducted in a state-of-the-art facility, which includes a software training lab and a fully functional machine training lab. Training is free with the original purchase of the OMAX waterjet.
Venables’ 55100 JetMachining Center is equipped to maximize time efficiency with an EnduroMAX® 40 horsepower pump, Tilt-A-Jet®, and a terrain follower. The EnduroMAX delivers the highest jet power in the industry for faster and more efficient cutting. The addition of the Tilt-A-Jet and terrain follower ensures that the programmed part is cut correctly the first time, every time.
With a waterjet onsite, over the past several years Venables has been able to further their reputation as a reliable and punctual manufacturing and fabrication shop. Wingerak states, “We knew at that time and continue to be reminded through continued knowledgeable support that placing our trust with the OMAX was 100% the correct choice for Venables when looking for a waterjet.”