Customer Success: Educational Institutions
Racing Towards The Future At UCLan With The MAXIEM 1515
Machine: MAXIEM 1515
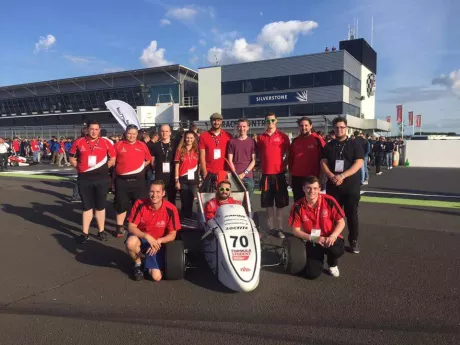
The roar of engines, the cheering crowd and a handbuilt race car ready to prove itself on the tarmac. Every year members of Formula UCLan put their best work forward to be a part of this experience. Formula UCLan is a group of engineering students at the University of Central Lancashire, or UCLan for short, dedicated to engineering and building motorsport race cars from scratch. The students do everything from developing CAD drawings to manufacturing the car, and then enter their new vehicle into events in order to see how it performs. The goal of the program is to provide these students with real hands-on experience and help them improve their reputation among potential employers. This year, the Formula UCLan entered their race car for use in the Formula Student Event, a motorsport event where student groups compete and put their race car creations to the test.
The University of Central Lancashire is dedicated to providing its students with the tools and experience they need to achieve a competitive edge for their developing careers. Recently the engineering department looked into adding CNC machines into their workshop to improve the students' experiences. They considered both laser cutting machines and abrasive waterjet machines, and at the time decided to go with the laser cutter. Upon gaining a better understanding of what the waterjet can offer they have now added a MAXIEM 1515 to the workshop. Paul Critchley, the Principal Technician of the LIS Workshop Services at UCLan, backs their decision by saying, “we came to better realize the merits of a waterjet such as ease of use and flexibility in terms of the huge variety of materials and thicknesses it can cope with.”
Adding the MAXIEM to their workshop resulted in new opportunities and helps the students to develop valuable skills. Paul notes that the "engineering students realized they could design parts differently knowing the capability of the waterjet machine." The students were able to redesign several of their parts and transition them from time-consuming CNC machining to the easy-to-use MAXIEM abrasive waterjet. The intuitive design of the software makes it easier for UCLan to teach a larger number of students how to use the abrasive waterjet. As a result, students can quickly take the parts they have designed and cut them out in the shop on the waterjet. Often times these parts require little or no further machining and are ready to be put in place, reducing the amount of time they spend waiting on experienced CNC machinists.
UCLan's abrasive waterjet is mainly used for motorsport projects such as Formula UCLan's race car, as well as eco vehicles and superbikes. Formula UCLan has been able to use the MAXIEM for a large number of their parts including a variety of steel brackets for the frame, aluminum wheel bearing housings, and even the brake discs. Due to the versatility of the waterjet, the workshop has also been able to help out with a few physics research projects cutting ceramics and silicates.
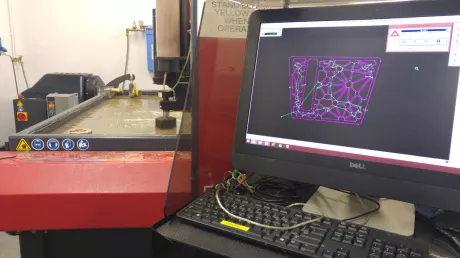
The largest benefits of the MAXIEM are the experience and skills that the students gain from using the machine. The staff at UCLan are dedicated to helping these students succeed in their futures and that includes offering access to the tools they need to gain an upper hand. The abrasive waterjet provides these students with a unique machine that opens up the opportunity to experiment with designs and materials. Paul states, "The MAXIEM is helping us to give our students the engineering design skills to consider effective methods of production during the design process. The effect of this is to give our students an enhanced reputation in the labor market and thus to be sought after by potential employers."
Using these skills and experience, the members of Formula UCLan were able to produce a working race car built with their own hands for the Formula Student event. There they were presented with several hurdles including rigorous scrutineering tests and a damaged driveshaft caused by an accidental collision. Overall, despite these challenges, the team was highly satisfied with their accomplishment and what they had learned from the experience. This project is meant to form these students in ways that will help them in the future. Paul believes this was accomplished, saying, "The engineering industry is demanding graduates with more practical skills and a much greater appreciation of production methods. The abrasive waterjet has played a key role in helping us to meet that demand."