Customer Success: Manufacturing
Forward-Thinking Fabricator Goes Solar
Machine: OMAX 55100
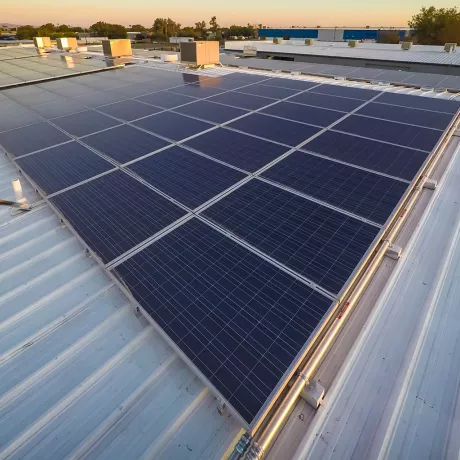
The owners of Creedbilt, Inc. have joined the leaders of some of the brightest, most competitive companies in America by choosing to power their business using solar energy.
Creedbilt, a family-owned custom fabrication shop in Glendale, Arizona, specializes in manufacturing custom truck bodies, hauler beds, flatbeds, and truck accessories. The full service shop runs press brakes, a ¼” x 12’ shear, bandsaws, tubing benders, a sheet metal roller, pneumatic tapping machine, hydraulic punch, welders, and an abrasive waterjet machine. The company operates 40 hours a week and powering all that machinery requires considerable energy.
A desire to run an environmentally friendly business, combined with rising electricity rates, led owners Jeremy and Jason Creed to do a cost-benefit analysis of converting the 10,000+ square foot Creedbilt facility to clean solar energy.
While average electricity rates are increasing across the country, the cost of installing a solar power system has dropped significantly in the past few years. In fact, the average price of a completed commercial PV (photovoltaic) project has declined 45 percent since 2012, according to a report from the Solar Energy Industries Association (SEIA). The Creeds estimated the solar panel energy system would pay for itself in about five years.
Recognizing the sound investment in both the environment and the business, the Creeds set to work at converting the facility to run on solar energy. They also decided to install the 186 rooftop solar panels and four inverters themselves. In July of 2014, Creedbilt’s solar energy system was put into service.
The shop is still connected to the grid. If the shop uses more power than the solar panels produce, it draws power from the grid. When the solar panels produce more power than the shop uses, the excess power is put on the grid. “In a week period, our system is tending to make more power than we consume,” says Jeremy Creed. And the local utility pays Creedbilt for those excess kilowatts. Based on the savings the company experienced during their first year after going solar, the conversion cost will “probably be recovered in 3-3 ½ years,” predicts Jeremy, which is even sooner than expected.
Creedbilt understands the importance of continually investing in innovative ways to reduce operating costs, keep the impact to the environment minimal, and keep business rolling in the doors. Another “green” investment the company made that achieved exactly that was the purchase of an OMAX 55100 JetMachining Center.
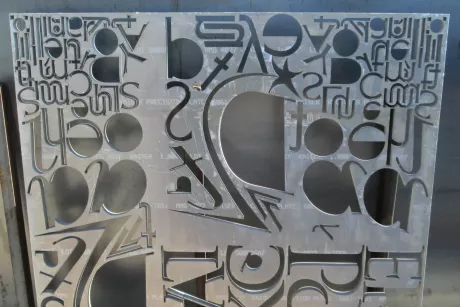
Abrasive waterjet cutting is an environmentally friendly industrial cutting technology. Unlike thermal processes such as plasma or laser, waterjet generates no noxious fumes during the cutting process. Waterjet cutting requires no cooling or lubricating oils, so there are no chemically contaminated chips to dispose of. The cutting "tools," water and garnet abrasive, are environmentally benign and available worldwide with minimal preprocessing.
In addition to being a “green” mechanical process, abrasive waterjet cutting also leaves behind a satin-smooth finished edge. Creedbilt’s primary goal with the abrasive waterjet system purchase was to shorten production time by reducing the need for secondary processes after cutting. “Our old method for cutting parts [using a plasma cutter] always had slag that had to be removed. Sometimes, this could require hours of de-slagging,” explains Jeremy. “Slag removal had become a major pain for us.” Cutting the same parts on the OMAX waterjet, the secondary processes have been eliminated altogether. “Everything out of the waterjet is super clean.”
Eliminating the need for secondary processing wasn’t the only benefit Creedbilt found with the addition of the abrasive waterjet system. “Our decision to purchase the OMAX 55100 solved more problems than we expected,” continues Jeremy. “It has boosted our quality a ton and actually helped cut costs on a lot of different parts we manufacture. We started finding ways to use the waterjet for locating holes in parts that we had previously drilled by hand.” Because the cutting head can be precisely positioned over the material, and that precise positioning is repeatable, the Creedbilt team found cutting holes in drawer fronts and brackets with the waterjet produced a superior end product. “The accuracy we can now hold on our truck bodies and parts is phenomenal compared to pre-waterjet bodies we built.”
Production has been further streamlined by using the abrasive waterjet to cut notches in parts, which previously required moving parts between different machines. “The waterjet has saved quite a few steps in almost everything we build.”
Due to the versatility of waterjet cutting, Creedbilt can now take on a wider variety of customers and orders. “We purchased the machine at the beginning of the last economic downturn,” says Jeremy, “and this machine brought in a lot of work that we would not have been able to do prior to owning the machine, which kept an income flowing during rough times.”
Going green with solar power and an OMAX abrasive waterjet system is paying off for this business dedicated to producing high-quality, competitively-priced products with minimal ecological impact.