Customer Success: Manufacturing
Norsk Titanium Improves Its Manufacturing Process with OMAX Waterjet
Machine: OMAX 60120
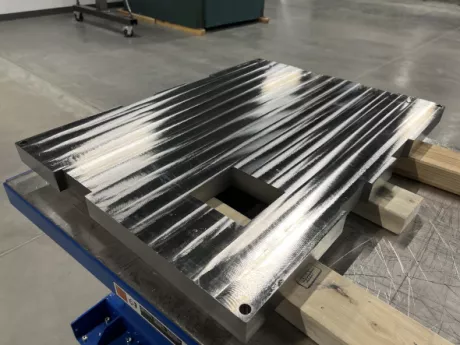
Norsk Titanium produces near net shape forging replacement parts for aerospace, defense, and industrial applications using a wire additive process called Rapid Plasma Deposition (RPD®). The company has a facility in Plattsburgh, NY, where it operates its RPD® machines and delivers its parts to customers worldwide.
One of the key steps in the RPD® process is to cut the raw material, which is titanium plate, into individual substrates sized to the geometry of the part to be printed. Previously, Norsk Titanium outsourced this step to a local vendor, which resulted in longer lead times, higher costs, and more material waste.
To overcome these challenges, Norsk Titanium decided to invest in a waterjet cutting machine. The waterjet cutter allows Norsk Titanium to cut its own substrates in-house, with more precision, speed, and flexibility.
The company chose to go out to bid and prepared a request for proposal with a basic specification for the waterjet cutter. The company evaluated the bids from different waterjet vendors and selected OMAX, a Hypertherm Associates brand, as the winner. The main factors that influenced their decision were the quality and features of the OMAX machine, such as the solid removal system and the ease of use of the software.
Norsk Titanium purchased the OMAX 60120 model with a 50 horsepower EnduroMAX direct drive pump, taper eliminating Tilt-A-Jet cutting head, IntelliMAX software and a solids removal system. The OMAX product line offers industry leading cutting accuracy and the EnduroMAX pump delivers fast and efficient cutting speeds. IntelliMAX software facilitates easy print to part processes, including broad part file compatibility and advanced cutting algorithms. The solids removal systems eliminate downtime by continuous removal of used abrasive during the cutting process.
“So far, we have been very impressed with the software that accompanied the OMAX machine. I can easily see this being an extremely daunting task to cut without good software.” Brian Lamoy, Production and Facilities Manager.
The OMAX IntelliMAX Software Suite, compatible with Windows 10, empowers users with exceptional control and efficiency. Seamlessly navigating from design to machining, IntelliMAX simplifies the process while delivering precision and speed. Tailored specifically for abrasive waterjet control, MAKE ensures unparalleled accuracy by orchestrating precise motor commands and optimizing cutting parameters. Real-time monitoring and predictive analysis further enhance productivity, whether on or off the shop floor. Every aspect of IntelliMAX is meticulously crafted to synchronize with OMAX hardware, enabling users to quote jobs with pinpoint accuracy and confidence. With MAKE's virtual cutting simulations, users can anticipate job durations accurately, eliminating guesswork and ensuring customer satisfaction.
The waterjet cutter also enables Norsk Titanium to explore and develop a more near net shape, which means that the substrate has a similar shape to the final part, rather than a rectangular shape. This reduces the amount of material that is machined, saving time and money for both Norsk Titanium and its customers.
“The OMAX 60120 allows us to precisely cut substrate in-house” said Steve Eaton, VP Operations, adding that “This results in 10-40% less plate material going to the machining center resulting in less time and cost at machining.”