Tips & Tricks
Factors of Speed
It is often asked "how fast is a waterjet?"
OMAX waterjets are faster than many cutting machines on the market. Exactly how fast depends on a number of factors. Power, material, thickness and more need to be considered when determining how long a finished piece will take to cut. For example, tool steel will have a different cutting time than titanium. The following are the main factors that affect the speed of OMAX machines:
Power of the Pump
Double the horsepower of the pump, and the cutting speed will dramatically increase. Horsepower determines how much water is actually flowing through the waterjet’s nozzle. Think of a 30 hp pump as a garden hose, and a 100 hp pump as a fire hose. If the goal is to move as much water as possible, efficiently, thereby inducting the abrasive into the stream and cutting, then the fire hose is going to be faster.
To learn more about how pumps affect your cutting speed, check out this article in the FABRICATOR.
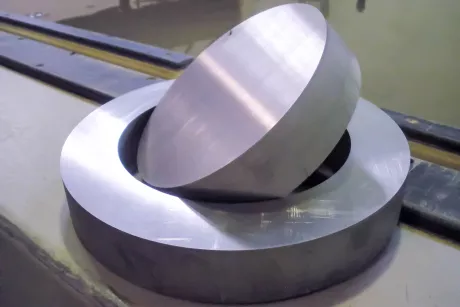
Material
In terms of types of material, an abrasive waterjet is the most versatile cutting method available. OMAX machines are currently being used to cut aluminum, brass, carbon fiber, glass-refined plastics, ballistics laminates and much more. With abrasive waterjets, there is no need for special coatings or other considerations. Materials simply need to be fixtured into place. The cut product has no heat-affected zones (HAZ) or material distortion, often removing the need for secondary machining.
Typically, the harder the material, the slower the cut. There are some exceptions to this: titanium generally cuts faster than steel on a waterjet. The thickness of the material is also a factor. Waterjets can cut any thickness up to the Z-height of the cutting head, but thicker materials will cut more slowly than thinner.
As long as the material in question is lower on the Mohr scale than your cutting medium, you can cut it.
Geometry of the Part
Simple parts are faster to cut than more complex parts, which is true for all industrial cutting methods. However, when you get into more complex shapes, the specifics of the cutting tool can make incremental changes that result in huge time savings.
A waterjet is a machine tool that shows its true benefit when cutting complex geometries on a variety of materials. For abrasive waterjets, hardware performance only provides a portion of the potential cutting performance returns. An optimal software controller is capable of ensuring exceptional precision throughout every angle and curve in a cut while increasing the speed of production and reducing the cost of consumables. To get the full value of your abrasive waterjet, you need the best hardware coupled with the best, most optimal software – and OMAX’s IntelliMAX software is the most advanced waterjet cutting controller on the market.
Desired Surface Finish
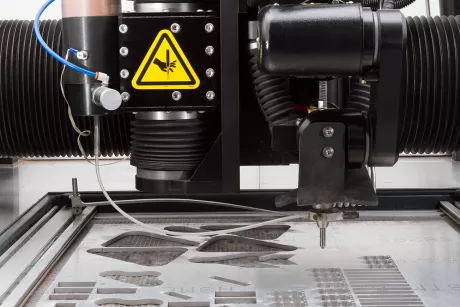
The higher the quality of a part’s surface finish after cutting, the longer it will take to make the piece. Due to its precision and high cut quality, many fabrication shops use their waterjet as a single-stop tool. This means the parts that come off the waterjet are ready for use without any secondary machining.
To save time, several manufacturers aim for lower quality surfaces because they plan to cut near-net shapes. Integrating this near-net shape cutting into processes significantly reduces production time. An abrasive waterjet can handle large sheets of raw material and cut multiple blanks with very little setup and fixturing time. Abrasive waterjets can easily cut material that’s difficult to machine on a CNC mill, such as Inconel®, Hastelloy® and titanium, and there’s no need to change tooling to cut different types of material.
Up-to-Date Software
OMAX is constantly refining its cutting models and implementing new, clever optimizations that speed up production. Take advantage of these by regularly updating your software. Software can make a huge difference, especially when compared with the non-OMAX machines your competitors may have – and with free updates for the life of the machine, it’s easy to keep systems fully updated for optimal cutting.