Tips & Tricks
Medical Shops Discover Waterjet Machining Versatility and Accuracy
Manufacturers of medical components are increasingly taking advantage of abrasive waterjet machining. It’s a versatile, accurate process that matches many medical partmakers’ needs while offering some capabilities that are unavailable from other machining processes. These manufacturers opt for waterjet machining mainly because it does not create a heat-affected zone that can compromise part performance.
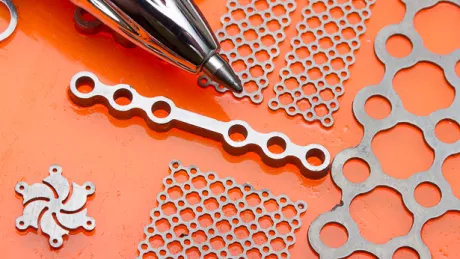
Additionally, medical applications often involve small, complex parts that can be difficult to clamp and hold steady against force generated during conventional machining. Waterjet cutting exerts practically zero force on the part being cut, reducing fixturing challenges to keeping clamps (if any are necessary) out of the cutting path. Waterjet machining’s ability to cut essentially any material is also a significant factor when considering the continually broadening range of workpiece materials utilized in medical components.
A waterjet can cut metals from steels to nickel-base alloys and non-metallic workpieces including carbon fiber, PEEK, graphite, composites, laminates and more. Reflective and non-conductive materials that pose challenges for laser and EDM machining are not a problem for a waterjet machine.
One example of a particularly challenging medical material successfully cut on a waterjet machine is the nickel-titanium alloy known as Nitinol. Called “memory steel,” it is flexible and can be bent and formed to acute shapes, but it also is formulated to return to its original shape when heated. Medical component manufacturers use the alloy to make parts like self-expanding vascular stents. The stents are compressed so they can be inserted into a blood vessel, then expand to their original shape to support the vessel when exposed to the 37˚C temperature of the human body.
For many Nitinol applications laser or conventional machining methods are not effective. Waterjet machining enables intricate stent designs to be cut from flat stock and then rolled into cylinders to fit inside a blood vessel. Even with very finely detailed parts, waterjet machining can eliminate conventional machining problems such as edge chipping and burrs that are problematic in medical parts.
In response to the need to produce small, precise parts in medical manufacturing and similar applications, we engineered our MicroMAX JetMachining Center. Because accuracy and consistency are equal in importance to the ability to process smaller parts, the MicroMAX machine features a 0.1-micron linear optical encoder system and provides positioning accuracy of less than 5 microns. The machine’s structure is highly rigid with low-mass bridges and carriages as well as vibration isolation of machine tables and gantries. It is designed for fully enclosed operation and work in clean room environments.
For increased accuracy, the machine offers medical manufacturers the option for cooling lines that connect to a chiller and maintain a consistent 70˚ temperature within the machine, eliminating heat-related variations in part sizes. Waterjet cutting itself does not generate heat, but the friction of the abrasive during cutting will gradually raise the temperature of the water in the machine tank. Shops that do not have to meet micron-level specifications may ignore a few degrees of temperature difference within the machining system, but users like medical or electronics manufacturers require consistent performance at those accuracies. The MicroMAX JetMachining center provides repeatability of ± 3 microns and accuracy of ± 13 microns across the machine table.
Because the medical industry is generally secretive about their parts and how they produce them, it can be hard to specify how they take advantage of waterjet machining. Potential users often won’t discuss a part’s function in detail but will send OMAX a file with minimal feature details to learn if the part is a candidate for waterjet machining. Medically related parts include but are not limited to stents, surgical tools, components that may be inserted in the body, and a variety of prosthetics. A recent OMAX project for a dental products company involved cutting tiny teeth on a vibrating multitool-type dental saw.
In many medical applications, manufacturers use a waterjet to produce a prototype then send the part out to a production company to be stamped, molded or cast for mass production. Additionally, workpiece material challenges may make waterjet the only way to produce a part. Depending on production volume and other considerations such as proprietary information issues, a medical manufacturer may cut the part on its own waterjet or send it to a supplier that has multiple machines.
Because the waterjet process does not require special hard tooling or CAM programming, a company without extensive 3D design experience can progress from a drawing on a napkin to viewing a model on computer screen within minutes. On the other hand, users familiar with 3D design are not limited to OMAX software. We work with all the major players in 3D software design and have developed plug-ins for our operational software. Users can download a part design, specify the material being cut and its thickness, and the part will be ready to cut. If a 3D model is available, our IntelliCAM software can generate either 2D or 3D toolpaths from it.
Waterjet machining’s versatility is driving its adoption through the medical industry and as well as similar applications. A user typically does not buy a waterjet to cut a single workpiece material. A machine used for Nitinol today, for instance, may cut titanium tomorrow and stainless steel the day after that. Part shapes and thicknesses are wide open as well. Unlike some old school machining methods, no stress is induced by the cutting tool. Plus, waterjet techniques can be complementary with other machining methods. For example, roughing a part out with a waterjet can be followed by conventional finish machining. New applications constantly appear because the manufacturers who use waterjet machining are limited only by their imaginations, not their machine tools.