Tips & Tricks
The New OptiMAX is the Future of Abrasive Waterjet Cutting Technology
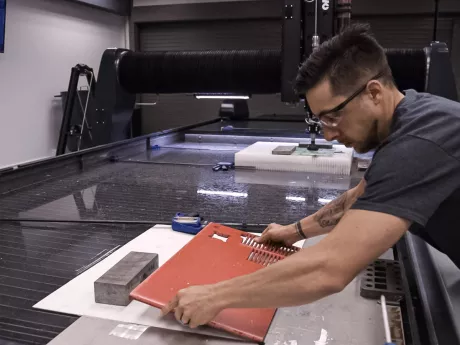
It’s hard to know if the engineers at OMAX can predict the future, but they certainly met it head-on with the new OptiMAX Precision JetMachining Center, the company’s most accurate and advanced abrasive waterjet to date.
As the culmination of three decades of engineering expertise and experience, the OptiMAX debuted in early March to take waterjet cutting to the next level, which is exactly what the industry needs in an age of increasing production demands and a serious lack of skilled operators. The flagship OptiMAX product line is designed to address specific industry pain points by providing the fastest processing speeds and high reliability with improved performance automation that makes it one of the most operator-friendly abrasive waterjets available.
OptiMAX machines are built from the outset for high throughput and high uptime operation that simplifies the process of cutting complex, tight-tolerance parts from almost any material with less dependence on highly skilled operators. System control and monitoring features like IntelliVISOR provide feedback to guide operators with real-time monitoring of temperature, pressure and cutting system status. In the event of an out-of-range excursion, the cutting system takes corrective action or notifies the operator to act, reducing the need for constant observation by operators and freeing them for other tasks or to tend multiple machines. IntelliVISOR also allows remote monitoring from anywhere via a desktop console or other mobile device.
Additionally, OMAX’s latest generation EnduroMAX direct drive pump further reduces operator dependence by automatically setting and autonomously maintaining correct pressure throughout the day’s cutting jobs. The pump’s Motorized Adjustable Dump Orifice (MADO) and Motorized Excess Flow Valve (MEFV) are also internally monitored and automatically adjusted with a pressure feedback loop.
A redesigned abrasive delivery system prevents clogged abrasive feed lines, one of the waterjet industry’s major pain points. Prior to the OptiMAX, clogged lines on a waterjet system required manual dismantling and cleaning, which resulted in unplanned downtime throughout the day. The new OptiMAX Air Sweep system prevents moisture contamination in the abrasive hopper and automates nozzle and feed line clearance. A fluid diverter and automatic flushing capability reduce the clog-clearing process from a 15-minute maintenance task to a 60-second automated procedure.
Maximizing output, minimizing downtime, and optimizing production while reducing dependency on highly skilled operators is what the OptiMAX Precision JetMachining Center is designed to do. Made for diverse manufacturers who need a versatile, user-friendly cutting system, OptiMAX is the future of abrasive waterjet cutting.