Tips & Tricks
Tips for IntelliETCH
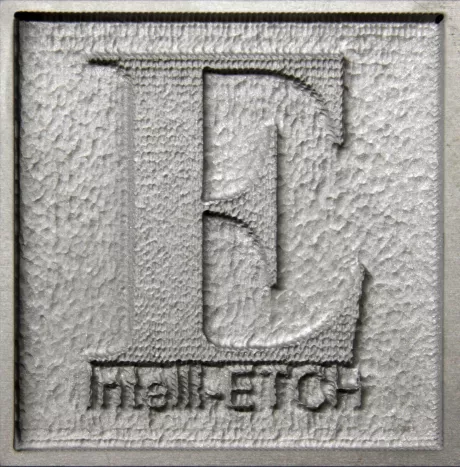
The IntelliETCH feature in IntelliMAX allows your waterjet to etch everything from simple part numbers to elegant artistic designs. However, performing more intricate work requires the machining head to accelerate and decelerate around corners, slowing down the process and increasing the material removal rate. Here are some tips for effectively using Etch for intricate work:
- Perform etching on smaller machines that can accelerate more quickly and the machining head won't slow down as much. This will reduce the excessive material removed in the corners.
- Use a lower pressure and reduce the abrasive feed rate. To achieve finer etchings, consider using the OMAX Dual Abrasive Flow Rate Kit, which uses a lower abrasive flow during low-pressure etching applications.
- Slow the entire process down to achieve the desired etch depth. Slower overall movement reduces the need for slowing down in the corners for more even etch depth.
- Vary the speed of multiple etches in the same path with XData: If you require different etching speeds, such as etches with varying depth levels, consider using XData to override the speeds with an absolute speed.
- When etching brittle material such as glass or granite, reducing the pressure is required to prevent cracking. Setting the pump to 20 ksi (140,000 kPa) or lower is ideal. Even 30 ksi (200,000 kPa) is too much pressure.
- Avoid sharp corners and the slowdown will be reduced – you won't dig into the material so much.
- By etching into a hard metal like steel instead of a soft metal like aluminum, the etching will be a lot cleaner and the corner digging will be less noticeable.
- Experiment with relay delays to prevent excess digging at the start and end of the cutting path. Try to prevent the jet from dwelling in the “On” state, which can drill tiny holes in the workpiece.
- Note that points where etch lines cross each other will be etched twice as deep.
- As you etch, the jet will lag, just as in cutting. Imagine that you are etching a square shape to a depth of 0.5" (1.3 cm). This will machine out a box-shaped area – with the bottom of the box skewed opposite of the jet’s direction. This is yet another reason to use lower pressure and slow the jet down. By etching over the same area multiple times, moving the cutting head back and forth, this effect can be cancelled out.
- For some materials, consider cutting a "mask" on the machine, then using the mask in conjunction with a sand blaster to remove the material on the final part.
- Etching becomes increasingly difficult or impossible when working with thin or soft materials. In thin materials, the jet is likely to cut all the way through. In soft materials, the jet will also likely cut all the way through, or dig deep into the corners of the drawing entities as the machine slows down.
- For artistic work and improved etch control over large areas, consider using OMAX IntelliETCH.