Tips & Tricks
Working with Titanium on a Waterjet
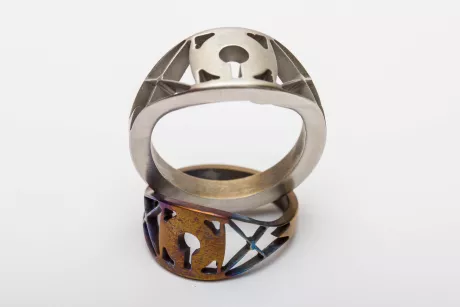
We often get asked, “Can an OMAX waterjet cut titanium?”
The answer is “Yes.”
Titanium is harder, but also lighter, than both aluminum and steel. If you have ever machined titanium on a mill, you know it has a tendency to be a very slow cut. However, with an abrasive waterjet, cutting titanium is fast and easy.
Here is a basic guide to working with titanium on a waterjet:
- Program your part in LAYOUT (OMAX’s CAD program)
- Move your part into MAKE (OMAX’s CAM program)
- Fixture your material
- Set your standoff of your nozzle accordingly
- Begin machining
It’s as simple as that.
Fixturing can be a time-consuming process on a mill. With a 5-axis, lathes, mills, etc. set-up time can be an average of 2.5 hours.
With a waterjet, fixturing and setup time are dramatically reduced. All you need to do is place the material on the tank slats, weigh the material down since the moving water under and around the piece cause the material to shift, and clamp it down. Waterjet fixturing and setup time should take approximately 15 minutes.
It is true that waterjet may not always be the best options for some parts. In this case, it might be a good idea to use a waterjet in near-net cutting before finishing the part on a 5-axis mill or other machine tool.
There is a financial advantage to cutting titanium with a waterjet as well. Since titanium is so expensive, a shop would generally like to have full-size remnants rather than turnings. It is likely that there will be usable/reusable material left over. Also depending on geographic location, you may find that recycling larger pieces of material brings in a greater return than turnings.
The best part about using an OMAX abrasive waterjet is that changing between materials is simple and quick. It only takes a selection from a material drop down. Change from cutting aluminum, to cutting titanium, to cutting anything other material out there with no special tooling considerations.