Tips & Tricks
Waterjet Cutting Saves Time and Money for Near Net Shape Production
For decades, parts makers have used near net shape production as an initial step to form parts and components very close to their final shapes. Near net shape has become more important with the increased use of expensive, exotic materials and the demand for leaner, more cost-efficient production. Abrasive waterjet is an ideal tool for the expanding industries that benefit from near net shape production.
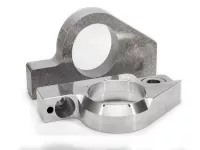
Benefits
Near net shape processing quickly cuts a rough shape of a part ahead of secondary operations that then bring the part to its final shape and finish. The process is fast, maximizes material usage, and is applicable to a broad range of materials, including metals, plastics, and composites.
Manufacturers in the aerospace and mobility sectors increasingly rely on the near net shape process to manufacture components made from expensive high-strength-to-weight materials such as titanium alloys and composites. These materials are difficult to machine and extremely hard on cutting tools. In some cases, the value of exotic material removed from the original billet can be more valuable than the resulting part. By employing near net shape techniques or partnering with shops that do, final component manufacturers extend tool life and save production costs. OMAX itself uses near net shape strategies to machine parts in-house for OMAX waterjet manufacturing, saving up to 40% on part production times.
OEMs have quickly discovered significant production cost savings by partnering with a shop that uses waterjet for initial production of its component blanks. Similarly, job shops can complement their existing manufacturing capabilities by adding waterjet to their processes.
Best Bet for Near Net
Abrasive waterjets are well suited for near net shape manufacturing because they can cut virtually any material at a wide range of thicknesses without creating a heat-affected zone or changing material properties, allowing for nesting multiple near net shapes into a single material piece. This allows for both fast part production and maximum material usage, reducing overall part costs.
At the same time, while exactness is not the aim of the near net shape strategy, waterjet technology is capable of precise cuts. OMAX waterjets can be highly accurate to an average of ±0.003 inches, which is more than sufficient for near net shape goals. A hybrid net shape/finished part can also be produced, further reducing production times, thanks to the precision of OMAX waterjets and the benefits of no material distortion from waterjet cutting.