Tips & Tricks
Why Waterjet Is The Best Method For Cutting Stainless Steel
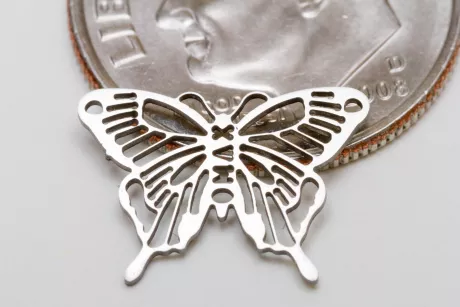
Almost every machine tool claims they are the best at machining stainless steel. For some applications, the tolerances achieved by most machine tools (and subsequent effects imparted by the machining) is fine. However, when a fabricator or prototype creator is looking to produce a high precision part, have it weld ready, or get it done now, there is really only one method – abrasive waterjets.
To help illustrate our argument, we’ll consider traditional CNC machining, as well as lasers and plasma, before examining the value-added benefits of cutting stainless with an OMAX abrasive waterjet.
Stainless steel is most often machined using conventional CNC mills and lathes. The biggest drawback to this is that stainless steel is very susceptible to work hardening. The machining process must be optimized to disburse heat to ensure work material isn’t distorted by heat-affected zones. In addition, the actual cutting tools, either high-speed steel or carbide, must always be kept sharp. After machining stainless steel on a CNC machine, an operator is often left with rough edges. To truly finish a part machined on a CNC, a file or deburrer secondary process is added.
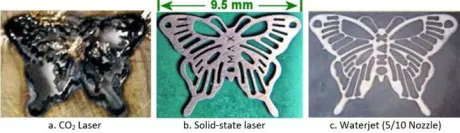
Lasers and Plasma cutters are often used to cut thin gauge stainless steel. The use of either of these methods involves extremely high heat. Plasma cutters are primarily rough cutting tools that require several secondary procedures to get a clean finish. CO2 laser is quick, but ineffective in fine details. Solid-state lasers are better for detailed cutting than CO2, but neither option is as effective as an OMAX abrasive waterjet.
With abrasive waterjet, cutting stainless steel is quick, easy and removes the need for many secondary processes. One of the most heralded benefits of abrasive waterjets is that it is a cold cutting process, meaning there are no heat-affected zones. This allows for a part that was cut on a waterjet to be welded immediately. Another huge benefit is that, since there is no material distortion due to heat, detailed work can be done to specification. Operators don’t have to concern themselves with the possibility of melting or gouging.
One of the biggest benefits of abrasive waterjet over laser or plasma is the thickness of the material cut. Laser cutting (both solid state and C02) is restricted to thinner gauges of stainless. On top of that, since stainless is reflective, it needs to be coated in a non-reflective film before laser cutting can occur. Though plasma doesn’t require special coatings for cutting, it still can only cut material about 1.25 inches thick before losing force and making a mess of the original material. OMAX abrasive waterjet can cut much thicker dimensions of stainless. It is not uncommon for fabricators to cut 6-inch-thick stainless steel part on their OMAX abrasive waterjet.